TESTING
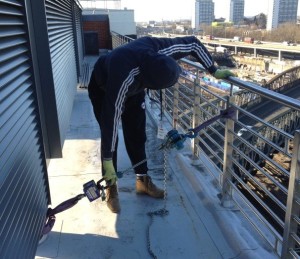
LOLER testing / Report of thorough examination – Inspection & Testing (aka test certs)
CLE’s trained & certified engineers offer testing and re-certifying for all major brands of lifting equipment to LOLER regulations – both on and off site. Specialists in Genie repair and testing, CLE offer a 48 hour turnaround service and flexible maintenance & testing contracts. CLE’s Barking, Wandsworth and St. Neots depots each have a specialized vacuum lifting facility with portrait and landscape ‘live load’ calibration and testing.
CLE’s preventative maintenance contracts are designed to meet your requirements for plant machinery, vacuum handling and lifting equipment offering out of hours service or time specific service for shut down periods-either on-site or at any of the four locations. CLE’s friendly, experienced engineers offer individual customers care.
What LEEA (Lifting Equipment Engineers Association) say about carrying our inspections in-house vs third party
- LOLER requires the competent person to be sufficiently independent and impartial to allow objective decisions to be made. With this in mind the question should really be, ‘can you check your own work?’ It is LEEA’s view that the answer to this question would depend on the complexity of the thorough examination.
- For example the thorough examination of a mechanically assembled chain sling following a repair is not a complicated task for a competent person to ascertain whether or not it has been assembled correctly. Whereas a thorough examination of a hoist following an overhaul of the lifting and braking mechanism is.
- Therefore the duty holder or the employer of persons doing the thorough examination should assess the risks in terms of complexity of the maintenance and subsequent thorough examination. The risk assessment should consider whether or not the examiner could be considered as being impartial given that the examiner is likely to assume that they have done a great job but perhaps not be as thorough as they ought to be. Sometimes a second pair of eyes will be better placed to act impartial and see defects associated with the maintenance.
- Note, human error is the root cause of a significant proportion of incidents.
- It is also important to note the BS 7121-2 series of standards state, ‘it is essential that the person that does the thorough examination is not the same person that did the maintenance.’
To see the original article from LEEA, please click here
Why Choose Concord Lifting for Inspection & Testing
-
1LEEA ACCREDITED – A COMPANY YOU CAN TRUST BACKED BY THE INDUSTRY GOVERNING BODYin 2015 Concord became a LEEA Development member-get your lifting equipment inspected by a company/personnel who know what they are doing backed by the industry governing body.
Have your lifting equipment and accessories inspected by a trusted and trained third party- eliminate the grey area of the operator inspecting his own work and have us take the risk and responsibility
-
2TIME/DATE GEO-LOCATION STAMPED PHOTOS OF EQUIPMENT BEING INSPECTEDThe Concord Engineers use a bespoke Concord Lifting Equipment system for carrying out reports of Thorough Examinations on a tablet which saves time and elimiates the risk of paperwork getting lost on site.
If there are pieces of equipment that he/she feels may require attention or they simply feel photo evidence should be stored relating to a piece of equipment, they will take photos or the equipment/scenario and our system will automatically time/date stamp and geo-location stamp the images, these images are attached to your CLE file and can be reviewed at a later date by you or anyone you chose.
-
3BOOK APPOINTMENT ONLINE, VIA EMAIL OR OVER THE PHONE-WHAT EVER IS EASIEST FOR YOUYou can either call us up or put the information on what needs testing/inspecting on this page (it takes about 30 seconds!) and we will confirm with you a date and time and who the engineer/engineers will be coming to do the inspection. Upon arrival the engineer will have the details needed and have paperwork ready to sign so everyone involved knows who what and when got done!
-
4HONEST & OPEN PRICINGWe do not have a minimum 1/2 day billing period-For inspection work we charge by the hour, so if you have 5 items that need inspecting or 30, if the equipment is easily accessible you can get great value for money.
if items fail/do not pass and they are easily repairable we will aim to repair onsite, failing that we can return the equipment back to a CLE depot and carry out the work there, or send an engineer out within 48 hours to fix the equipment. Prices for onsite inspection are £55 per hour, or lower if you decide to take up an optional service/repair plan with us. Simple repairs and also included in the price
-
5ELECTRONIC REMINDERS/TACKLE STORE MANAGEMENT- NEVER LOSE A TEST CERT!When the CLE engineer is inspecting your equipment, he updates our system live from his tablet, and as soon as an item successfully passes the test, we have a copy of Your Report of Thorough Examination on file-We will email you a copy of the test cert within 24 hours of the test being completed, and you can rest assured that we always have a copy of the test cert should you misplace it and can deliver it to you within 1 business day should you require it.
More importantly we will email you 1 month prior to equipment being due for inspection to remind you that equipment is due for another test so we can arrange to keep it covered and in service!
The format and layout of the Report of Thorough Examination are in the exact format outlined by LEEA, so they are easily recognizable and understandable by anyone familiar with these reports
-
6EMAILED TEST CERTS INSTANTLYDon’t worry about the test certs getting lost on site!
If you are an account customer as soon as our engineer is finished the inspection he/she will update our system and we will be able to email you an official copy of your Report of Thorough Examination within minutes-
Not an account customer? An engineer can either run your credit/debit card from their tablet to take payment when the job is done and create an invoice or call up to the office to do the same thing, either way within minutes of completion you will receive the test cert, invoice and receipt of payment
-
7WE COME TO YOUHoists, beams, equipment that is always in use, why take it out of service? leave your equipment working and we bring all the tools and equipment needed to carry out a report of Thorough Examination keeping the down time to a minimum
Our engineers all have CSCS cards and have years of experience with the equipment (working ‘on the tools’ on the workshop for a minimum of 3 years before going onsite and having shadowed senior staff for a minimum of 6 months before going out on customers site on their own.
We can also arrange test out of normal business hours to keep your project moving without delay
-
8CLEAR LABELING/TAGGING OF EQUIPMENTAll equipment should have its safe working load and any other critical information clearly visible at all times, if for some reason these details have work off we apply a durable weatherproof sticker with this information on there and a QR code/simple link to our mobile optimized website so the operator can view the operating instructions from any phone (iPhone, Android, Windows phone etc) tablet or desktop
Also for a nominal fee we will put tamper proof tags on the equipment in a color coded system, i.e blue tags expire January, red expire February which has the safe working load/requirement information on the tags on the equipment.
On-site Inspection /testing
CLE offers 3, 6 and 12-Monthly inspections to Lifting operations and Lifting Equipment Regulations 1998 (LOLER) designed to meet your company’s needs. CLE specialise in the testing of a variety of products including Gantries, Lift shaft/Motor room beams, Overhead cranes and Swing Jibs.
All CLE technicians are fully qualified in the examination and testing of a variety of products and always carry a comprehensive range of testing equipment needed to test your equipment on site.
After the thorough testing is complete, our technician will leave your with a hand written and signed proof of certification in line with the Health and Safety At Work Act (1974). Upon their return to CLE office, this information is uploaded to our secure server, and replicated to a printed certificate which is delivered to you via email, fax or post – allowing you to obtain copies from us in the future at no extra charge, and for CLE’s Account Managers to send you friendly reminders when equipment is next due for testing.
Repair & Maintenance
CLE’s preventative maintenance contracts are designed to meet your requirements for plant machinery, vacuum handling and lifting equipment offering out of hours service or time specific service for shut down periods either on site or at any of the four locations. CLE’s friendly, experienced engineers offer individual customer care
Contact us for all your testing needs now
Want to discuss testing? please call the depot closest to you/ your testing site and we will be more than happy to advise on requirements; alternatively you can email the relevant department/person at the specific depot and someone will get back to you straight away.
- Wandsworth wandsworth.testing@concordlifting.co.uk
- Barking barking.testing@concordlifting.co.uk
- Charlton charlton.testing@concordlifting.co.uk
- St Neots stneots.testing@concordlifting.co.uk