Inspection
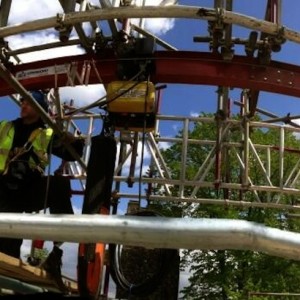
Inspection – Report of Thorough Examination Carried out on site or at Concord Depot
All Lifting equipment and accessories are required to have a current Report of Thorough Examination in order to be used. Depending on the equipment the reports are due every 3, 6 or 9 months-the most common frequency for inspection is 6 months. One of the benefits of hiring from Concord Lifting Equipment is all equipment is issued with a current Report dated from the first day of the hire and if your hire exceeds the length of the certificate we will re-certify the equipment for free.
We have multiple operatives working throughout the UK carrying out Reports of Thorough Examinations on customer
Book your Inspection work in now –
Have equipment that needs inspection? spend 30 seconds filling out this form and we will get back to you straight away with a quote, it doesn’t matter if you have worked with us before or not!
Benefits of Concord carrying out your testing, Inspection and Report of Thorough Examination
- Easy Pricing No hidden costs – The majority of our inspection work is charged out on a per hour basis, how every long the travel time is and how long it takes to carry out the inspection is what you will get charged. There is no minimum half day charge. If it takes 25 minutes to get there, 25 minutes back and 10 minutes to do the work you will be charged just for 1 hour.
- Years of Experience – Our operatives carrying out the inspection have years of experience, all onsite inspectors have to carry out a minimum of a years work in one our depots ‘on the tools’ repairing and servicing our hire equipment before they go onsite to inspect other peoples equipment
- Simple Repair included in the price – Where possible if equipment looks as though it will fail its report of Thorough Examination our operative will do what they can to repair the equipment onsite for you for the same price. If the repair is more technical we will give you a no obligation quotation free of charge to repair the equipment to bring it up to standard
- Preferential pricing on replacements – If repairing equipment is not safe or uneconomical you will get a discount on the new equipment required.
- Clear labeling and instructions – All equipment should have its safe working load and any other critical information clearly visible at all times, if for some reason these details have work off we apply a durable weatherproof sticker with this information on there and a QR code/simple link to our mobile optimized website so the operator can view the operating instructions from any phone (iPhone, Android, Windows phone etc) tablet or desktop.
- Tagging – For a nominal fee we will put tamper proof tags on the equipment in a color coded system, i.e blue tags expire January, red expire February which has the safe working load/requirement information on the tags on the equipment
- Managed reminders/ Safe keeping of all reports of thorough Examination – We all know what it is like, you get a test cert and file it somewhere and then 2 months later come to use the equipment and cannot find the cert! Our operatives create the report of thorough Examination electronically onsite and it is instantly uploaded to our secure server where it is checked by our office staff to make sure everything is as it should be. It then creates a reminder which will email you 1 month prior to when the inspection is next due. But more importantly you can rest assured that if the equipment is labelled/tagged we have the report of thorough examination on file and will email you an electronic copy within minutes of request normally but a maximum of 1 business day. If it is within its dates you can use the equipment
Why Choose Concord Lifting for Inspection & Testing?
-
1LEEA ACCREDITED – A COMPANY YOU CAN TRUST BACKED BY THE INDUSTRY GOVERNING BODYin 2015 Concord became a LEEA Development member-get your lifting equipment inspected by a company/personnel who know what they are doing backed by the industry governing body.
Have your lifting equipment and accessories inspected by a trusted and trained third party- eliminate the grey area of the operator inspecting his own work and have us take the risk and responsibility
-
2TIME/DATE GEO-LOCATION STAMPED PHOTOS OF EQUIPMENT BEING INSPECTEDThe Concord Engineers use a bespoke Concord Lifting Equipment system for carrying out reports of Thorough Examinations on a tablet which saves time and elimiates the risk of paperwork getting lost on site.
If there are pieces of equipment that he/she feels may require attention or they simply feel photo evidence should be stored relating to a piece of equipment, they will take photos or the equipment/scenario and our system will automatically time/date stamp and geo-location stamp the images, these images are attached to your CLE file and can be reviewed at a later date by you or anyone you chose.
-
3BOOK APPOINTMENT ONLINE, VIA EMAIL OR OVER THE PHONE-WHAT EVER IS EASIEST FOR YOUYou can either call us up or put the information on what needs testing/inspecting on this page (it takes about 30 seconds!) and we will confirm with you a date and time and who the engineer/engineers will be coming to do the inspection. Upon arrival the engineer will have the details needed and have paperwork ready to sign so everyone involved knows who what and when got done!
-
4HONEST & OPEN PRICINGWe do not have a minimum 1/2 day billing period-For inspection work we charge by the hour, so if you have 5 items that need inspecting or 30, if the equipment is easily accessible you can get great value for money.
if items fail/do not pass and they are easily repairable we will aim to repair onsite, failing that we can return the equipment back to a CLE depot and carry out the work there, or send an engineer out within 48 hours to fix the equipment. Prices for onsite inspection are £55 per hour, or lower if you decide to take up an optional service/repair plan with us. Simple repairs and also included in the price
-
5ELECTRONIC REMINDERS/TACKLE STORE MANAGEMENT- NEVER LOSE A TEST CERT!When the CLE engineer is inspecting your equipment, he updates our system live from his tablet, and as soon as an item successfully passes the test, we have a copy of Your Report of Thorough Examination on file-We will email you a copy of the test cert within 24 hours of the test being completed, and you can rest assured that we always have a copy of the test cert should you misplace it and can deliver it to you within 1 business day should you require it.
More importantly we will email you 1 month prior to equipment being due for inspection to remind you that equipment is due for another test so we can arrange to keep it covered and in service!
The format and layout of the Report of Thorough Examination are in the exact format outlined by LEEA, so they are easily recognizable and understandable by anyone familiar with these reports
-
6EMAILED TEST CERTS INSTANTLYDon’t worry about the test certs getting lost on site!
If you are an account customer as soon as our engineer is finished the inspection he/she will update our system and we will be able to email you an official copy of your Report of Thorough Examination within minutes-
Not an account customer? An engineer can either run your credit/debit card from their tablet to take payment when the job is done and create an invoice or call up to the office to do the same thing, either way within minutes of completion you will receive the test cert, invoice and receipt of payment
-
7WE COME TO YOUHoists, beams, equipment that is always in use, why take it out of service? leave your equipment working and we bring all the tools and equipment needed to carry out a report of Thorough Examination keeping the down time to a minimum
Our engineers all have CSCS cards and have years of experience with the equipment (working ‘on the tools’ on the workshop for a minimum of 3 years before going onsite and having shadowed senior staff for a minimum of 6 months before going out on customers site on their own.
We can also arrange test out of normal business hours to keep your project moving without delay
-
8CLEAR LABELING/TAGGING OF EQUIPMENTAll equipment should have its safe working load and any other critical information clearly visible at all times, if for some reason these details have work off we apply a durable weatherproof sticker with this information on there and a QR code/simple link to our mobile optimized website so the operator can view the operating instructions from any phone (iPhone, Android, Windows phone etc) tablet or desktop
Also for a nominal fee we will put tamper proof tags on the equipment in a color coded system, i.e blue tags expire January, red expire February which has the safe working load/requirement information on the tags on the equipment.
Information on LOLER Requirements for Lifting Equipment Safety & Inspection
Requirements That LOLER 1998 Places On Employers and Workers
LOLER 1998 essentially puts in place four key protocols that all employers and workers must abide by:
- All equipment must be safe and suitable for purpose The manufacturer must identify any hazards associated with the equipment in question, they must then assess these hazards to bring them down to acceptable levels. All lifting equipment is normally put through an independent type testing process to establish that it will safely perform the tasks required to one of the below standards. • BS (British Standard, used mainly in the UK) • ISO Standards (International Standard) • EN (Euronorm, used throughout Europe) • CEN/CENELEC (Euronorm Standards) The above standards are a published specification that establishes a common language and contains a technical specification or other precise criteria. They are designed to be used consistently as a rule, guideline or definition.
- All personnel must be suitably trained. All manufacturers of lifting equipment are obliged to send out instructions for use of all products. The employer is then obliged to make sure employees are aware of these instructions and use the lifting equipment correctly. To achieve this the employees must be competent. Competence is achieved through experience, technical knowledge and training.
- All equipment must be maintained in a safe condition. It is good practice for all personnel using lifting equipment to conduct a pre-use inspection on all items. Regulation 9 of LOLER also outlines specific requirements for the formal inspection of lifting equipment at mandatory intervals. These inspections are to be performed by a competent person and the findings of the inspections recorded. Maximum fixed periods for thorough examinations and inspection of lifting equipment as stated in regulation 9 of LOLER are: •Lifting Accessories – 6 Months •Lifting Appliances – 12 Months •Man Riding Equipment – 6 Months Or in accordance with a written scheme of examination. Any inspection record must be made in line with the requirements of schedule 1 of LOLER The only exception to this is: If the lifting equipment has not been used before and; In the case of lifting equipment issued with an EC declaration of conformity, the employer has possession of such declaration and it is not made more than 12 months before the lifting equipment is put into service.
- Records must be kept for all equipment. All equipment manufactured should be given a “birth certificate”. This should prove that when first made, it complied with any requirement. In Europe today, this document would normally be an EC Declaration of conformity plus a manufacturers certificate if called for by the standard worked to.